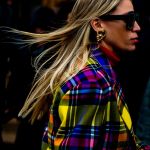
Why local manufacturing might be the solution to supply chain problems
A simple answer to a seemingly insoluble problem
December 30th, 2021
Today, Hugo Boss announced that it will expand the presence of its workers and factories in Europe, specifically in Turkey, to shorten the supply chain and not have to depend on factories in Southeast Asia. The brand will increase by a third the staff of its smart factory in Izmir and will also invest in industrial tools and machines to avoid, as the Financial Timeswrites, «supply shortages, delays and higher shipping costs». The brand's CEO, Daniel Greider, explained: «Our future strategy is to produce even more garments close to those markets where they will be sold». A choice that, according to Grieder, has already brought enormous competitive advantages to the company and that, read in a broader sense, constitutes a very simple solution to the supply chain problems that have plagued the fashion industry since the beginning of the pandemic. A few months ago, for example, Nike had to cancel many of its customers' orders due to supply chain delays, while WWD estimated that the same problems cost GAP $152 million this year alone. All problems that derive only from the length of these supply chains, which start from raw materials pass from Asia and then arrive in the West – with considerable economic expenditure but also consumption of fossil fuels for transport.
Hugo Boss' idea of shortening the supply chain seems counterintuitive at first, as on an economic level the production costs in Asian factories are much lower than those in Europe – nevertheless the Covid pandemic has shown that the complicated mechanism of customs, shipments and synchronization of orders and productions is functional but also very fragile. A type of critical issue that can be circumvented with an apparently trivial solution such as shortening the supply chain itself, reducing the very possibility of delays but also, in terms of communication, reassuring consumers who, as is known, tend to invest more resources in goods produced more or less locally or in any case in Europe than in items from factories around the world.
The benefit of a shorter supply chain also lies in sustainability. In an article published on BoF, it is highlighted how the communication around the idea of a lean supply chain is more about reducing costs than that of the length of the supply chain in physical terms, especially in a post-Covid world where «shipping costs have spiked amid scarce capacity, material prices and wages are rising in Asia, and so are costs of compliance and transparency». According to the article, it is the philosophy behind materials and shipping logistics that needs to change, especially given that the supply chain makes up 96% of fashion's footprint on the environment – with a lack of investment in sustainability by suppliers due to increased costs and a lack of incentives. A shorter production chain could certainly reduce this problem. But as the article explains:
«Supplier-led capabilities exist to supersede cost-driven practices for inflexible lean practices and lowest prices. The real essence of partnership is equal commitment to create a more productive, profitable and sustainable industry. The key to these imperatives to de-risk a needlessly high-risk business resides upstream in global manufacturing, regardless of geography. The high cost of low-cost fashion is no longer affordable or sustainable — and too costly to continue».